01 止口的含义
止口结构,在产品结构设计上也是一种常见的结构,对于有经验的工程师那是再熟悉不过了,然后对于初学者来说,他们并不一定知道,更谈不上理解,所以,为了帮助初学者理解,对止口的概念稍加文字介绍。
止口:止,从字面上理解是停止、禁止、限制的意思,比如说适可而止、浅尝辄止、望梅止渴;而在产品结构上通常表示限位的意思(即限制零件的移动,主要是对X轴和Y轴的限位,Z轴方向的限位通常通过螺丝或者卡扣之类的联接结构限位),由于其在结构上是一对凹凸结构,有点像人合上的嘴巴,所以称为止口。
02 止口的结构形式
止口的一般分类:
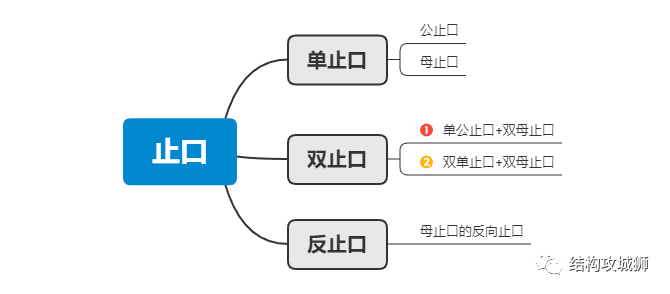
1、单止口:
为最常见的止口,由公止口和母止口组成,从外形上看是一对凹凸的结构,这对凹凸结构分别设计在两个配合的零件上,沿着侧壁内边凸出来的部分(加胶)称为公止口,沿着侧壁内边切掉凹下去的部分(减胶)称为母止口。公止口一般设计在壁厚较薄的壳体上,母止口一般设计在壁厚较厚的壳体上。
因为母止口需要往内切掉一部分胶厚,把母止口设计在壁厚较厚的壳体上可以有足够厚度被切除。这里需要注意的是,
2、双止口:
是相对于单止口而言,双止口实际上是由两个正反的单止口合并成新的止口,主要有以下两种结构形式:1)单公止口+双母止口,这种形式主要应用于上壳体厚度较薄,且对外观段差有要求的结构,下壳的双母止口可以限制上壳往里和往外的变形。
2)双公止口+双母止口,
这种形式主要应用于上下壳体厚度都较厚的结构,这种结构在外观上的段差可以控制很小,这种结构也称为密封性止口结构,,如做防水结构,中间增加胶圈或超声波焊接可起到防水作用;如做喇叭音腔,中间加泡棉也可起到密封音腔的作用,但此种止口结构要求壳体壁厚较大,一般需要2.5mm以上,否则母止口外缘就比较薄,外观容易产生厚薄印(应力痕)。
3、反止口:
也称反插骨,反限位的意思,反止口为母止口的反向止口,一般配合单止口一起设计,主要用于上下壳体都较薄的结构,反止口实际上是双母止口的简化,因为壳体没有足够壁厚去做双母止口,通过设计局部的筋位,所以通常反止口有以下几种结构形式。
(其作用跟止口差不多,都能起到对上下壳限位作用,不同的是止口一般都是整圈的,而反止口是整圈做若干骨位。止口和反止口一般都是放在一起设计的。)
1.反止口的形式1)单反止口,
这种反止口一般用于小型零件,结构简单,缺点是强度不够。
2)双反止口,
这种反止口较为普遍,最为常用,成对设计是为了保证强度。
3)这种止口主要用于空间不够的零件,没法做双反止口,此种止口强度好,缺点是结构没双止口简单,但也不失为一种好结构。
4)这种止口也是用于空间不够的零件,没法做双止口,此种止口缺点是需要在另一个壳上切出相应的母止口,胶厚突变外观有厚薄印(应力痕)风险,设计时注意圆角缓和过渡。
2.下面以第一种反止口为例来说明下止口间的主要配合尺寸
**
A:反止口的宽度,不能太小,太小强度不够,最好不少于一个壁厚;
B:反止口的高度,一般不少于1mm也不要高于分型面太多,骨位太高模具加工困难;
C:反止口倒C角,可利于装配,一般做到C0,5~C1.0;
D:反止口与公止口之间间隙,一般做到0.05~0.1即可,不建议零间隙配合,因为模具不一定做得很准,试模出来后产品一般都跟图上有点误差,如零间隙配合,后面就没有加胶的余地了;
附:反止口的设计原则是哪里需要就设计在哪里,即外壳需要限位的地方,特别是外观有要求的产品,就要多设计反止口。反止口的数量根据产品外形大小来定,如结构允许,应整圈均匀分布,优先设计成双止口,两组止口之间的距离一般为30到40mm,注意避开扣位,不能离扣位太近,否则扣位变形困难。
03 止口的作用
理想的外壳是不需要拆件的,但在现实中,需要考虑到制造工艺以及装配工艺(DFMA),外壳需要拆分成若干零件,相邻两个互相配合的零件之间就会存在结合缝隙,那零件结合处为什么需要设计止口?
首先通过以下三个生活中的例子,你就很容易理解止口结构所起到的作用。
- 为了防止厚薄印(应力痕),切掉的部分厚度和深度不能太大;
- 如果无法避免应力痕,外壳若做白色(纹面或高光面)应力痕基本不太明显,做黑色高光面效果稍好些但还是不能完全消除,黑色纹面效果应力痕是较严重的。
图二:冬天洗澡,寒风从门缝吹进来
以上现象是因为门与门框之间没有形成严密的止口结构,对于产品设计来说,是不希望产品出现这样的情况,因而目前不少公司都在致力于无缝隙(少缝隙)的拆件结构,即一体化结构设计,这方面尤其以苹果公司产品为代表。
比如以下苹果的某款电源设配器,常规的设配器采用的是上下壳,然后通过超声波焊接,但是上下壳之间会存在接缝,如下图左边两款;下图右边款采用的是塑胶Unibody工艺,外壳一体注塑成型,中间的夹线通过后期打磨去除,几乎看不到痕迹。
有关于塑胶一体化设计的更多相关介绍,可以点击这篇文章查阅:Unibody一体成型工艺(塑胶篇)。
虽然塑胶一体化设计好处多多,但是成本高(包括设计成本、模具成本、后处理成本等),对于普通的产品来说,采用上下壳拆件的方式还是目前主流,但是两个互相配合的零件之间需要设计止口,止口所能起到的作用如下:
1、起到遮蔽的作用,
两个相互配合的壳体本身是存在一条缝,对于容易变形的塑胶件,如果没有止口结构,由于缝隙不均匀,即使是功能没问题,但从外观上看就让人感觉低端,质量差,缝隙大点的话甚至可以看到里面的零部件。
2、起限位作用,
防止或减小两个相互配合的壳体装配时产生偏位或段差。如果两个相互配合的壳体零件长宽(XY)两方向设计有止口,那么这两个零件在XY方向上是互相被限位的,也可以理解成定位,这是有利于装配的;同时,还可以在特定方向上矫正零件的变形,如下图,A壳限制B壳往里(红色箭头方向)变形,同时B壳限制A壳往外(黑色箭头方向)变形。
以上为单止口,A壳有可能往里变形,B壳有可能往外变形,如果B壳上设计有反止口,那么AB壳互相限制对方往里或往外变形,可以有效控制外观段差。
3、起到密封作用,
4、起到防静电(ESD)作用,
上面已经有提到,一个理想的一体化壳体是不需要拆件,也就能达到密不透风的,静电也就无从而入,当然不会有静电问题了。但实际的壳体在配合处一定会有缝隙,所以一定存在ESD隐患。
如果将释放的静电看成是洪水的话,那么主要的解决方法与治水类似。可能很多项目处理ESD的方法不尽相同,但最终都可以归结为三条方案,“堵”—“疏”—“绝”。
其中,“堵”的方法属于机械结构方法,即在AB壳的结合处设计一圈止口,止口的作用就是起到静电墙作用,将静电隔离到外壳之外,让静电难以直接进来,即使有部分强度较大的能穿透进去,也因止口的作用使得这部分静电的能量大大减弱。(需注意的是设计时尽可能保留整圈止口的完整,保证完整的静电墙)
如果止口附近有电路板,尽量增加壳体的厚离,即增加外壳到电路板之间的距离D,根据经验,10kV的ESD在经过4mm至5.00mm的距离(此距离包含壳体的壁厚)后能量一般衰减为零。
或者通过一些等效方法增加壳体气隙的距离,这样可以避免或者大大减少ESD的能量强度,下图中,把电路板移高到公止口侧,增大了气隙距离,(如果电路板高度无法改变,可以通过把上下壳的止口对换,同样可以增大气隙距离)。
04 止口的设计原则
- 功能原则
- 外观质量原则
- 加工工艺原则
1、功能原则
1)合理选择止口结构形式
设计止口时首先要明确止口所起的作用,因为不同的止口结构形式多起到的作用不尽相同,比如,需要密封结构,那么优选双止口结构;如果壳体的壁厚较薄,那么优选单止口结构;如果需要起到防静电作用,那么应尽量保留整圈止口的完整性。
2)反止口的设计在保证本身功能同时不能影响其他结构功能
反止口应对称布置且间距合理,同时应避开卡扣位置(不能离扣位太近,否则扣位变形困难)
2、外观质量原则
1)外观段差
由于塑胶件易变形以及尺寸偏差大等缺点,同时这些缺点还受到塑胶材料、结构、模具、注塑工艺等诸多因数的影响,因此接缝处的段差控制一直是一个棘手的问题。
以下是较常用的单止口结构主要配合尺寸(仅供参考,部分尺寸取值范围应根据实际产品情况做适当调整):
A:公母止口配合面间隙尺寸,一般做到0.05~0.1即可;(由于塑胶难做到高精度,且存在变形,太小容易干涉,太大起不了作用)
B:公母止口避空尺寸,防止止口干涉,一般做到0.1~0.2;(因为公母止口接合处已做零配,此处做避空即可)
C:公止口倒C角,可利于装配,一般做到C0.3~0,5;
D:母止口过渡圆角,此处胶位厚度变化较大,做圆角可以减小外观应力痕,一般做到R0.3~0,5;
E:公止口高度,一般做到0.8~2mm,具体看制品大小;
F:母止口外观面胶厚,应大于壁厚的一半,否则此处外观容易产生应力痕;
G:反止口的宽度,不能太小,太小强度不够,最好不少于一个壁厚;
H:反止口的高度,一般不少于1mm也不要高于分型面太多,太高意义不大,保证有一定有效配合高度(减去斜角高度后)即可;
K:反止口倒C角,可利于装配,一般做到C0,5~C1.0;
N:反止口与公止口之间间隙,一般做到0.05~0.1即可,不建议零间隙配合,因为模具不一定做得很准,试模出来后产品一般都跟图上有点误差,如零间隙配合,后面就没有加胶的余地了。
其中,以上尺寸A和尺寸N是影响段差控制比较重要的尺寸,对于小型产品来水,取0.05-0.1基本能满足要求;对于中大型产品来说,此两个间隙尺寸的取值应根据外壳的最大外形尺寸的公差值进行调整,因为对于注塑件来说,外形尺寸越大,其公差值就较大,如下表。
所以,对于小型产品,其外形尺寸变化小,即使有小超差或局部小变形,也能通过止口和反止口(即尺寸A和尺寸N)把变形部分拉回合理范围,减小外观段差。但是对于大中型产品,其外形尺寸变化大,很难通过止口和反止口控制段差处于很小范围,因此,对于这类产品,一般通过在接缝处设计美工线,使得段差跨度增大,减小刮手感。
对于超差过大的外壳,即使止口结构能够拉回部分外形,也会导致其他部分变形,最后整个段差会不均匀,这也是不能接受的,因此,控制段差最重要的是把外形尺寸管控好,使其能够适应所设计的止口间隙。
2)外观应力痕
应力痕,即厚薄印,常出现在壁厚变化过大处,由于收缩不一致,导致存在收缩应力,收缩应力把较薄处的塑胶往里拉,在外观上就会看到类似凹坑的印子,也可理解为收缩痕。
以上止口尺寸中,E(公止口高度),也对应母止口的深度尺寸,不宜太大,同时,F(母止口外观面胶厚),应至少为壁厚的一半,否则此处外观容易产生应力痕。
3、加工工艺原则
1)模具加工工艺
反止口筋位直接的间距不能太小(一般3mm以上),保证此处的模具钢料有足够强度。
2)成型工艺
公止口的宽度不能太小,太小成型困难且强度不够,建议一般取0.6以上。
END
特别声明:本文内容为整理、编辑、原创,部分图片内容来自于网络,只用于学习交流,如涉及版权问题,请联系删除,以上内容如有错误,欢迎留言指正,谢谢!