行星齿轮减速机组成、意义及特点
行星减速机主要传动机构为:太阳轮、行星轮、外齿圈
行星减速机因为机构原因,单级减速最小为3,最大一般不超过10,常见减速比为3,4,5,6,8,10。减速机奇数一
般不超过3级,但也有部分大减速比定制减速机有4级减速。
相对其他减速机,行星减速机具有高刚性、高精度(单级可做到1分以内)、高传动效率(单级在
97~98%)、高扭矩/体积比、终身免维护等特点。
因为这些特点,行星减速机多数是安装在步进电机和伺服电机上,用来降低转速、提升扭矩、匹配惯量。
减速机额定输入转速最高可达18000rpm(与减速机本身大小有关、减速机越大、额定输入转速越小)以上,
工业级行星减速机输出扭矩一般不超过2000Nm,特制超大扭矩行星减速机可做到10000Nm以上,工作温度一般在-25℃到100℃左右,通过改变润滑脂可改变其工作温度。
减速机的重要概念:
级数:行星轮的套数。由于一套行星轮无法满足较大的传动比,有时需要2套或者3套来满足较大的传动比要
求。由于增加了行星轮的套数,减速机的长度会增长,效率会有所下降。
回程间隙:将输出端固定,输入端分别顺时针和逆时针旋转至扭矩达到额定扭矩-/+2时,减速机输入端有一
个较小的角位移,此角位移就是回程间隙,单位为分。也有称作背隙。
行星减速机是一种用途广泛的工业产品。其性能可与其他军品级减速机产品相媲美,却有着工业级产品的价
格,被广泛应用于不同的工业场合。
行星减速机是一种具有广泛通用性的新性减速机,内部齿轮采用20CvMnT渗碳淬火和磨齿。整机具有结构尺
寸小,输出扭矩大,速比在、效率高、性能安全可靠等特点。本机主要用于塔式起重机的回转机构,又可作为配套部件用于起重、挖掘、运输、建筑等行业。
行星减速机产品特点:
行星齿轮减速机重量轻、体积小、传动比范围大、效率高、运转平稳、噪声低适应性强等特点。减速机广泛应用于冶金、矿山、起重运输、电力、能源、建筑建材、轻工、交通等工业部门。
产品说明:
1、P系列行星齿轮减速机采用模块化设计,可根据客户要求进行变化组合,
2、减速机采用渐开线行星齿轮传动,合理利用内、外啮合、功率分流,
3、箱体采用球墨铸铁,大大提高了箱体的钢性及抗震性,
4、齿轮均采用渗碳淬火处理,得到高硬耐磨表面,齿轮热处理后全部磨齿,降低了噪音,提高了整机的效率和使用寿命。
5、行星减速机P系列产品有9-34型规格,行星传动级数有2级和3级。
减速比:
25~4000r/min(与RX、R、K系列组合可达到更大速比)
输出转矩:2600000Nm
电机功率:0.4-12934kW
安装形式:
1、底脚安装
2、法兰安装
3、扭力臂安装。
出轴方式:
1、实心轴
2、渐开线花键实心轴
3、开线花键空心轴
4、带胀紧盘空心轴
润滑及保养:
在行星减速机中装入建议的型号和数值的润滑脂。行星减速机采用润滑油润滑。对于竖直安装的行星减速机,鉴于润滑油可能不能保证最上面的轴承的可靠润滑,因此采用另外的润滑措施。
在运行以前,在行星减速机中注入适量的润滑油,润滑油的粘性根据以下列表选择。行星减速机通常装备有注油孔和放油塞。因而在订购行星减速机的时候必须指定安装位置。下表列出了一般应用中建议采用的润滑油的牌子和型号。
注意:对于非常规工作条件的应用,请征询制造厂的意见。
工作油温不能超过80℃。
终生润滑的组合行星减速机在制造厂注满合成油,除此之外,行星减速机供货时通常是不带润滑油的,并带有注油塞和放油塞。本样本中列出的行星减速机润滑油数量只是估计值。根据订货时指定的安装位置设置油位塞的位置以保证正确注油,减速机注油量应该根据不同安装方式来确定。如果传输功率超过减速机的热容量,必须提供外置冷却装置.
行星减速机包括单级、双级和三级传动,计有12个机座,27个型号,58种速比,可组成498台不同规格的减速机。
本减速机主要用于冶金、矿山、起重运输、石油化工、煤炭能源、水泥建材、工程建材、工程建筑等行业。亦可用于轻工纺织、水利水电等部门作减速或增速传动。
NGW行星减速机包括单级、双级和三级传动,计有12个机座,27个型号,58种速比,可组成498台不同规格的减速机。
本减速机主要用于冶金、矿山、起重运输、石油化工、煤炭能源、水泥建材、工程建材、工程建筑等行业。亦可用于轻工纺 适用条件:
减速机齿轮传动圆周速度不超过10米/秒。
输入轴转速不高于1500转/分。
减速机工作环境温度-40℃-+45℃。
减速机可用于正、反两向运转。
行星齿轮减速机工作原理:
1)齿圈固定,太阳轮主动,行星架被动。 此种组合为降速传动,通常传动比一般为2.5~5,转向相同。
2)齿圈固定,行星架主动,太阳轮被动。此种组合为升速传动,传动比一般为0.2~0.4,转向相同。
3)太阳轮固定,齿圈主动,行星架被动。此种组合为降速传动,传动比一般为1.25~1.67,转向相同。
4)太阳轮固定,行星架主动,齿圈被动。此种组合为升速传动,传动比一般为0.6~0.8,转向相同。
5)行星架固定,太阳轮主动,齿圈被动。传动比一般为1.5~4,转向相反。
6)行星架固定,齿圈主动,太阳轮被动。此种组合为升速传动,传动比一般为0.25~0.67,转向相反。
7)把三元件中任意两元件结合为一体的情况:当把行星架和齿圈结合为一体作为主动件,太阳轮为被动件或者把太阳轮和行星架结合为一体作为主动件,齿圈作为被动件的运动情况。行星齿轮间没有相对运动,作为一个整体运转,传动比为1,转向相同。汽车上常用此种组合方式组成直接档。
8)三元件中任一元件为主动,其余的两元件自由:从分析中可知,其余两元件无确定的转速输出。第六种组合方式,由于升速较大,主被动件的转向相反,在汽车上通常不用这种组合。其余的七种组合方式比较常用。
行星减速机的安装方法:
在减速机家族中,行星减速机以其体积小,传动效率高,减速范围广,精度高等诸多有点,而被广泛应用于伺服、步进、直流等传动系统中。其作用就是在保证精密传动的前提下,主要被用来降低转速增大扭矩和降低负载/电机的转动惯量比。在过去几年里,有的用户在使用减速机时,由于违规安装等人为因素,而导致减速机的输出轴折断了,使企业蒙受了不必要的损失。因此,为了更好的帮助广大用户用好减速机,向你详细地介绍如何正确安装行星减速机。
正确的安装,使用和维护减速机,是保证机械设备正常运行的重要环节。因此,在安装行星减速机时,请务必严格按照下面的安装使用相关事项,认真地装配和使用。
行星轮端面磨削
在汽车齿轮的磨削工艺中有一种工艺是先磨削齿轮内孔,再磨削齿轮的端面。而在磨削齿轮端面的过程中,一般采用双端面磨床进行磨削。但是在新型的汽车齿轮磨削要求中,发现原有的双端面磨削齿轮端面的工艺,不能满足内孔与端面的垂直度要求。 并且这种双端面磨削工艺不利于单个工件的流转,而且不利于齿轮大加工余量的端面磨削。<br />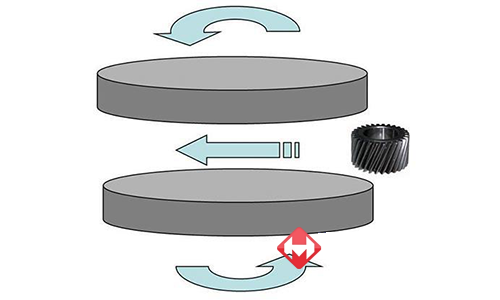<br /> 在高精度汽车齿轮的应用中,为了消除齿轮在运动过程中的震动,齿轮的内孔与端面的垂直度要保证在10μm以内。在先磨削内孔-再对齿轮的双端面进行磨削的工艺中,双端面磨削不影响内孔与端面的垂直度,但是双端面磨削只能保证垂直度在0.025mm以内的垂直度要求,这种双端面磨削工艺保证的垂直度不能消除齿轮震动。如果采用Nagel 机床他能够在一台设备中完成内孔的珩磨及端面磨削,并且保证内孔与端面的垂直度在10μm以内。<br /> 在全球齿轮磨削中先磨削内孔在磨削端面的工艺中,如果要保证垂直度要求,要先以基准面为基准磨削另一个端面,然后在将工件翻过来磨削另一个端面。才能保证工件10μm的垂直度要求。接下来我们介绍一下Nagel 机床的磨削过程:<br />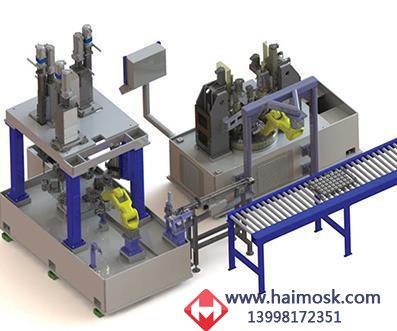<br /> <br /> 首先齿轮工件要在Nagel EC0 中珩磨齿轮内孔。齿轮珩磨内孔的磨削工艺:粗加工,半精加工和精加工三种工艺一次磨削完成。在每个这三种珩磨工序后都有在线测量系统检测磨削齿轮,并且砂轮自动补偿和修整。 <br /> 然后在Nagel SPV 中磨削齿轮端面,珩磨完内孔的齿轮被输送到SPV磨削工序,这种spv端面磨削工序一共有四个工位:上下料工位、磨削齿轮第一个端面工位、齿轮反转180°工位、磨削跌第二个端面工位。每个工位都有在线测量装置检测齿轮的厚度尺寸。磨削完成的工件被下料道成品输送带上。<br /> 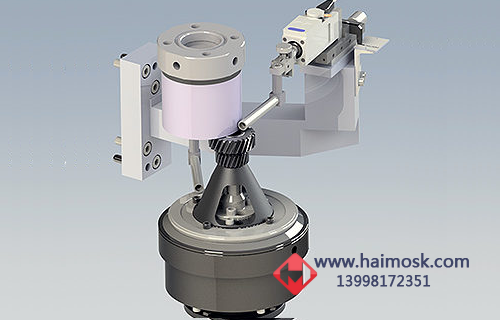<br /> <br />采用Nagel 机床磨削齿轮内孔及端面数据:<br /> <br />
材质 | 粉末冶金 |
---|---|
磨削位置 | 孔和端面 |
磨削余量 | 0.025 to 0.100 mm |
内孔直径 | 30 ± 0.005 mm |
粗糙度 | 0.10 μm |
平面度 | 0.003 mm |
垂直度 | 0.005 mm |
圆度 | 0.005 mm |
直线度 | 0.005 mm |
在国外的这种先磨削内孔在磨削端面的磨削工艺中保证垂直度,其实非常类似国内齿轮内圆磨削加工中经常会用到的工艺就是现采用内圆磨床磨削内孔,再采用单端面磨床磨削齿轮端面,从而保证齿轮的垂直度。
粉末冶金行星轮端面磨削
目前粉末冶金齿轮普遍应用在汽车发动机中,此种粉末冶金齿轮通过一次成型和精整工艺。由于此粉末冶金齿轮的内孔及端面的垂直度高,所以现有的双端面磨床的磨削工艺难以达到要求,故采用单端面磨床磨削一面再磨削另一面的磨削工艺!<br />**粉末冶金齿轮单端面磨床磨削原理及CBN砂轮
由于此粉末冶金齿轮的B面要保证与内孔垂直并且要求两个齿轮的端面平行度控制在0.003mm以内,所以本次磨削采用单端面磨床磨削,由于齿轮的外径不大,内孔16mm,所以采用15环的树脂CBN砂轮进行磨削。
粉末冶金齿轮图纸要求
粉末冶金齿轮内孔:16mm;厚度:19.97mm;材质:粉末冶金;硬度:HRB80;平行度:0.003mm;平面度:0.003mm;粗糙度:RZ4;垂直度:0.006mm
粉末冶金齿轮单端面磨床磨削现场情况**
加工难点:此粉末冶金齿轮的双端面磨削的加工难点在于内孔与B面的垂直度0.006mm保证困难,由于内孔已经加工完成,且现有的无论是双端面磨床磨削工艺还是双端面磨床磨削工艺都无法保证垂直度0.006mm的精度要求。采用海默单端面磨床磨削次工件完全可以保证工件原有内孔与端面的垂直度不受破坏,从而保证垂直度。
粉末冶金齿轮单端面磨床磨削检测情况
**粉末冶金齿轮单端面磨床磨削结果
单端面磨床磨削结论:**
1.本次单端面磨床磨削粉末冶金齿轮一共42件,针对42件工件进行抽检的结果为:粉末冶金的齿轮B面的平面度均保证在0.002mm以内,粉末冶金齿轮的两个端面平行度均在0.002mm以内;粉末冶金齿轮的两个端面的尺寸均在19.97-19.65mm之间,符合客户齿轮公差0-0.005mm的要求;粗糙度在RZ1-RZ1.66z之间,完全满足粗糙度RZ4的要求。
2.从以上磨削数据中,如调整CBN砂轮的粒度,增大磨削力,磨削节拍还有优化的空间。
3.后期可以实现单端面磨床自动上下料功能,以提高加工效率;
进口多轴超精端面磨床磨削齿轮工艺
多轴超精端面磨床
国外的一种高效的过工位磨削齿轮端面的工艺,在一台设备上可以完成磨削齿轮的第一个端面的半精加工、精加工、去毛刺及第二个端面的半精加工、精加工、去毛刺的工序。
第一工位:上下料工位
该工位是上下料工位,通常我们可以选择采用手动上下料、机械手上下料更或者是机器人上下料。 第二工位:半精加工
为了保证齿轮内孔与端面的垂直度及两个齿轮端面的平行度,可以采用砂轮进行磨削齿轮端面,由于工件轴及砂轮轴不在一个中心线上,可以通过砂轮与工件轴调节倾斜角度来实现工件表面的平面、中凹、中凸等。 第三工位:精加工
精加工工位采砂轮粒度更小的砂轮进行精加工,达到齿轮精度要求。
第四工位:去毛刺
去毛刺工位是采用毛刷对工件进行去毛刺处理,从而达到去毛刺的效果。 第五工位:反转工位
工件在经过上料、第一个面半精加工、第一个面精加工、去毛刺工序后通过翻转工位对工件进行180°翻转磨削工件的第二个端面。在第六个工位进行第二个面的半精加工、在第七个工位进行精加工、在第八个工位进行去毛刺。从而完成齿轮端面磨削的全部工序,并且保证齿轮的垂直度。
国外单端面磨床解决内孔与端面垂直度的方法
国外单端面磨床
在齿轮端面磨削的过程中通常为了提高加工效率而选择双端面磨床,但是由于很多齿轮的内孔与端面的垂直
度都会要求保证在0.01mm以内。为了保证0.01mm以内,通常加工工艺是先车削内孔与端面,利用车削的端面为基准磨削另一个端面,再利用磨削的第一个端面为基准磨削车削过的端面。但是国内的双端面磨床无法保证0.01mm的垂直度。
在上述视频中采用的是双轴双工位磨削齿轮端面,机械手同时针对双工位进行上料,同时进行下料。采用普
通刚玉砂轮。虽然采用了双工位磨削但是上下料机械手加长了工件单件节拍,采用刚玉砂轮磨削齿轮端面,需要经常更换砂轮,也降低了加工齿轮端面的磨削效率。
海默单端面磨床加工齿轮的端面,采用的是单轴双工位磨削,一个工位上料,另外一个工位下料,充分利用
了上下料时间。而且使用305mm直径CBN砂轮,CBN砂轮的修整周期长、使用寿命长、降低了更换砂轮的频次,更适合齿轮端面的磨削。